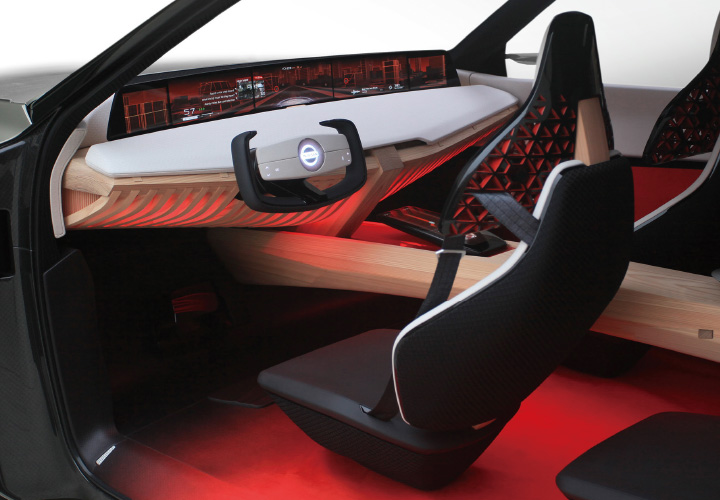
Mobility Parts
環境に優しいものづくりで
自動車の新しいラグジュアリーを創造する
天童木工では家具製造で培った成形合板による
木材加工技術をベースに、1987年より天然木を使った
モビリティパーツ(自動車内装部品)の製作を開始しました。
同年、ホンダ レジェンドに納品した内装パネルは、
量産車では日本初となる本杢自動車内装部品となります。
以来、天童木工が製造した内装パネル、ステアリングなどは、
これまでホンダ、トヨタ、日産、いすゞなどの
大手自動車メーカー各社で採用されております。
また自動車業界の喫緊の課題となっている
脱炭素社会への取り組みや廃プラスチック問題
そしてSDGsといった活動へ貢献できる「ものづくり」の実現に向けて、
サスティナブルマテリアルである木材だけではなく
バイオマス原料であるセルロース系繊維を使用した
新たなモビリティパーツ(自動車内装部品)の研究を進めております。
天童木工の基幹技術「成形合板」について
成形合板とは、薄くスライスした単板と呼ばれる木材に接着剤を塗布し、それらを重ね合わせて治具と呼ばれる型に入れ、圧力と熱を加えることで様々な形をつくり出す技術です。芯材の単板に用いるブナ材は、広葉樹の中でも水分を多く含んでおり弾力と反りが出やすいため、一般的な家具作りでは不向きとされていました。しかし技術の進歩や長年の試行錯誤により、その特性を上手く利用する方法を確立しました。成形合板にすることで、同じ厚みの無垢材と比較し約1.5〜2倍まで強度を高めることができるのもメリットの一つです。
また成形合板に使用される単板は、原料となる丸太を“カツラ剥き”のように厚さ1mm程度に切り出すため、木材を無駄なく使えます。さらに、どんなに複雑な形でも設計の段階から計算し、必要な形を効率的にカットできることもあり、同じ木材から家具の材料として使える割合は無垢材の約40%に対して成形合板は約80%と言われています。
強くて美しく、使い心地の良い家具を量産できる成形合板は、自然由来の木材のロスを減らせるサスティナブルな製造技術という側面も持ち合わせています。モビリティパーツ(自動車内装部品)の技術には、成形合板による家具づくりで培ってきた経験が、さまざまな形で活かされています。
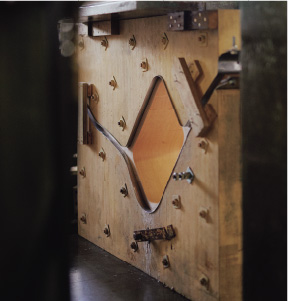
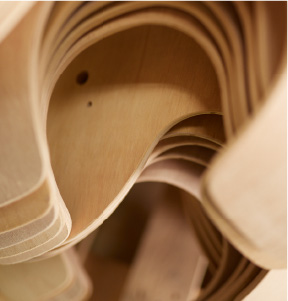
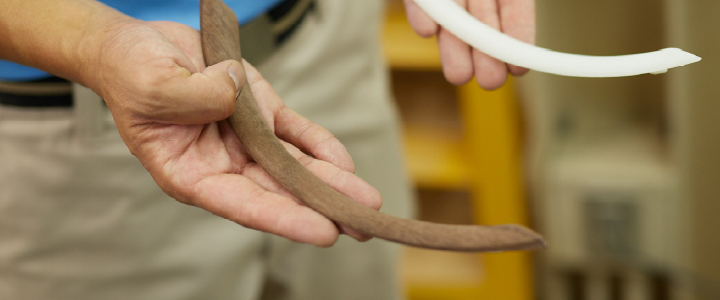
モビリティパーツ製造技術
モビリティパーツ(自動車内装部品)の技術紹介
高い精度、耐久性、美しさ、そして環境への配慮etc.
これからのモビリティパーツ(自動車内装部品)に求められる
新しい価値を生み出す当社の代表的な製造技術を紹介します。
天童木工の成形合板による家具づくりにおいては「接着」がとても重要な工程となりますが、複雑な形状でも精度高く仕上げなければならないモビリティパーツ製造では、この3次元立体成形(真空プレス)がまさに肝心要の技術となります。
成形合板技術を応用する形で、当初は木材やアルミの平面に突板を貼ることから始まった技術ですが、試行錯誤を繰り返すことで現在ではインストルメントパネル(インパネ)をはじめとする複雑な3次元形状はもちろん、樹脂にも厚さ0.2mmの突板を貼り込むことが可能です。
樹脂基材に木材の表面材を高精度かつ剥がれないように貼り付けることは非常に難易度が高い技術ですが、独自に開発した接着技術により高い耐久性と美しい仕上がりの両立を実現しました。当社で手掛けたパーツがリコールやサービスキャンペーンの対象になった例は一度もありません。

木の繊維は木目方向に曲げることは可能ですが、木目と反対の方向に曲げようとすると割れてしまいます。一般的に自動車のステアリングは、手で握るため円柱の形状を楕円形に成形します。そのため天然杢の突板シートを自動車のステアリングに綺麗に貼り込むためには、ハンドル部分の丸い形状に合わせて杢目を縦方向に貼ることが標準的でした。
そこに登場したのが縞杢(しまもく)です。縞杢は天然杢の突板を積層し、木目方向から90度の角度でスライスすることで人工的に縞模様を表現した突板シートです。この「縞杢」の突板シートをステアリングの形状に綺麗に貼り込み、尚且つ水平方向(横方向)にして貼り込みたい、という依頼がメーカーのデザイン部門から舞い込みました。
自動車を運転する際、ステアリングは絶えず触れている部分であり、身体に一番近い場所です。そのため僅かなシワやキズ、模様の乱れなどは目につきやすく、とても気になります。木材は革のように柔らかくないので、シワなくきれいに貼り込むだけでも高度な技術が必要です。天童木工は試行錯誤を重ねて、突板シートがシワにならない最適形状を探り当て、カットしたシートを模様の乱れなくステアリングに接着させる横方向杢目接着技術を開発しました。
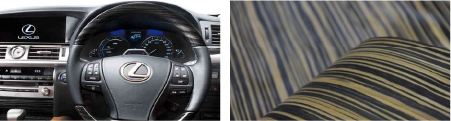
天童木工では、サスティナブルマテリアルである木材だけではなく、バイオマス原料となるセルロース系繊維を使用したモビリティパーツ(自動車内装部品)の研究開発を積極的に進めています。
その一例として、いすゞ フォワード/エルフの本杢パーキングブレーキカバーでは、2019年より脱炭素社会の観点から従来のカーボン繊維ではなくフラックス繊維を芯材として採用しています。
このように、従来の環境負荷の大きい素材をフラックス繊維などの自然由来素材に置き換えることで、サスティナブルなものづくりを可能とする技術です。

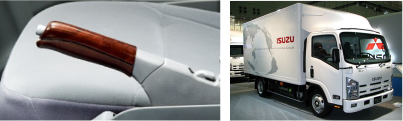
1本の角材からスライスした単板を、そのままの構成(配置)で成形することによって、成形合板の特徴を活かしながら、無垢材同様に杢目の連なった美しいステアリングの製造を可能とする技術です。これにより、杢目による表現の可能性がさらに広がります。
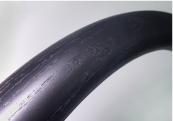
木材と異種素材を高精度で接着する技術を活用し、アルミ(金属)と積層接着した突板(木材)部分だけをレーザー加工機で削り取ることで、金属ならではの光沢をデザインに活かすことが可能な技術です。
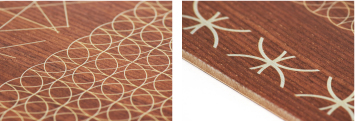
天童木工では、熱に強く、加工しやすく、環境にも優しい自然由来の新素材として近年注目されている改質リグニンを含有させたバイオプラスチックによるインサート成形技術の開発に取り組んでいます。
セルロース系繊維同様、従来の環境負荷の大きい素材を改質リグニンを含有したバイオプラスチックに代替することで、サスティナブルなものづくりが可能となります。
リグニンは、すべての木材に重量ベースで20%~35%含まれる成分です。木材の中の繊維同士を接着して、固くしっかりとした構造にするための物質で、抽出されたリグニンは強固で耐熱性を示すなど高い機能性があることがわかっています。天童木工ではリグニンの中でも、他の樹木に比べて構造のバラツキが少ない特徴を持つスギ由来の改質リグニンについて研究を進めています。
スギは日本固有の樹木であり、日本国内の樹木の中で最も多く、林業・林産業におけるサプライチェーンも確立されているため、均一な改質リグニンを安定して生産することが可能です。
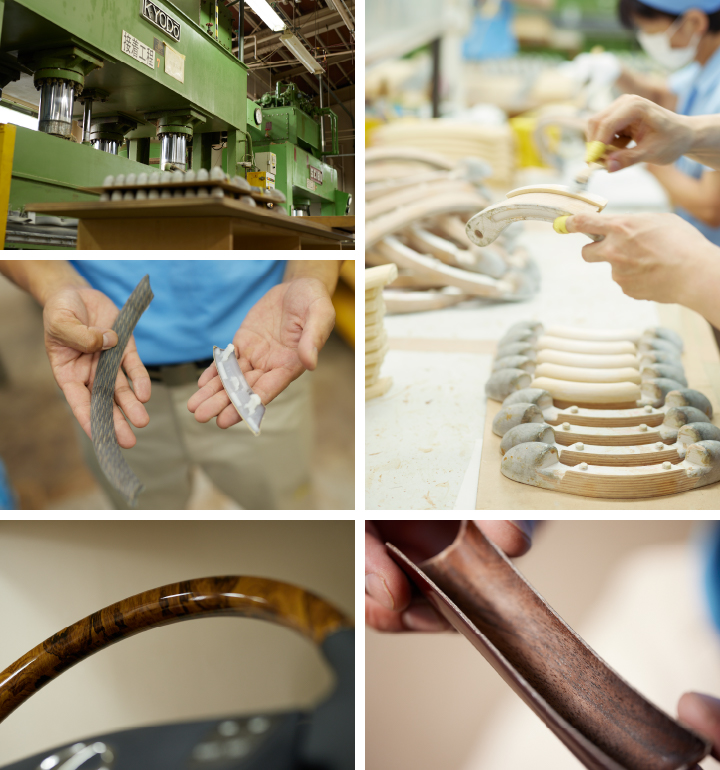
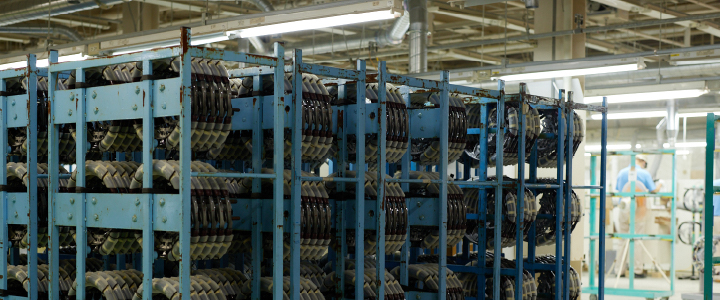
生産管理と研究開発
確かな品質、スピード、安定供給、そして新しい素材や技術の提案etc.
資材調達から製造、研究開発まで自社で行う一貫生産体制で
量産車はもちろん、一点もののショーモデルやプロトタイプなどあらゆるニーズにお応えします。
世界中に広がるネットワークを駆使した調達力
天童木工では、ウォールナットやローズウッドといった銘木から、環境に優しい素材として期待されているヘンプ繊維(麻)やフラックス繊維(亜麻)などのセルロース系繊維まで、モビリティパーツ(自動車内装部品)に使われる素材はすべて自社調達が可能です。世界中から厳選した丸太や細かな玉杢が美しいバールと呼ばれる根の部分は、モビリティパーツの素材として使えるようになるまで、およそ1〜5年間、自社工場でじっくり天然乾燥させています。家具づくり同様、材料調達から最終的な自動車内装部品の製造まで、すべて自社で完結できるのは天童木工の大きな強みです。
木材を知りつくした職人による製造力
天童木工のモビリティパーツ(自動車内装部品)は、1987年の初代ホンダ レジェンドに採用された本杢ウッドパネルからスタートしました。以降、手掛けた内装パネル、ステアリングなどは、ホンダ、トヨタ(レクサス)、日産、いすゞなどの大手自動車メーカー各社で採用されてきました。要求される精度や耐久性が家具とは桁違いに異なるモビリティパーツ分野への参入は、木を知りつくした職人の存在があったからこそ実現しました。技術と経験、そしてイノベーションを積み重ねてきた専属の職人による製造力は、天童木工の大きな強みです。
ブレークスルーを引き出す開発力
天童木工では、家具やモビリティパーツ(自動車内装部品)の製造の枠に留まらず、その時代に合った技術と自由な発想を掛け合わせることで、新しいニーズや可能性にチャレンジし続けています。国産のスギやヒノキに新たな可能性を付与する「Roll Press Wood」は、その一例です。また近年では、自動車産業でも関心の高いサスティナブルなものづくりへのシフトに向け、セルロース系繊維や環境に優しい自然由来の新素材として注目されている改質リグニンを含有させた高機能バイオプラスチックの研究開発にも、専属の開発チームを組織し積極的に取り組んでいます。クライアントの課題や社会問題の解決につながるブレークスルーを引き出す開発力は、職人による製造力と両輪をなす天童木工の大きな強みです。
デザイナーの理想を具現化する対応力
天童木工のアイコンとも言える柳宗理がデザインした「バタフライスツール」は、1954年当時、その複雑な曲面を実現できる工場がなく、仙台の産業工芸試験所の紹介で柳が天童木工を訪れたことから始まりました。柳の描く図面の形状を実現するのに約3年の時間を要しましたが、天童木工の職人たちは「できない」とは言わず試行錯誤を繰り返した末、厚さわずか7.5mmの2枚の成形合板を真鍮金具でジョイントしただけのスツールに、美しさと強度を宿すことに成功しました。「“できない”とは言わない」。1940年の創業以来、代々受け継がれる天童木工のDNAに刻まれた精神は、モビリティパーツ(自動車内装部品)の分野にもしっかりと受け継がれています。天童木工が誇る3次元立体成形(真空プレス)も横方向杢目接着も、理想を追求するデザイナーの要求に「“できない”とは言わない」ことで実現し磨かれた技術です。量産車から1点もののプロトタイプ、そしてショーモデルまで、デザイナーの理想を具現化するこの対応力もまた、天童木工の大きな強みです。
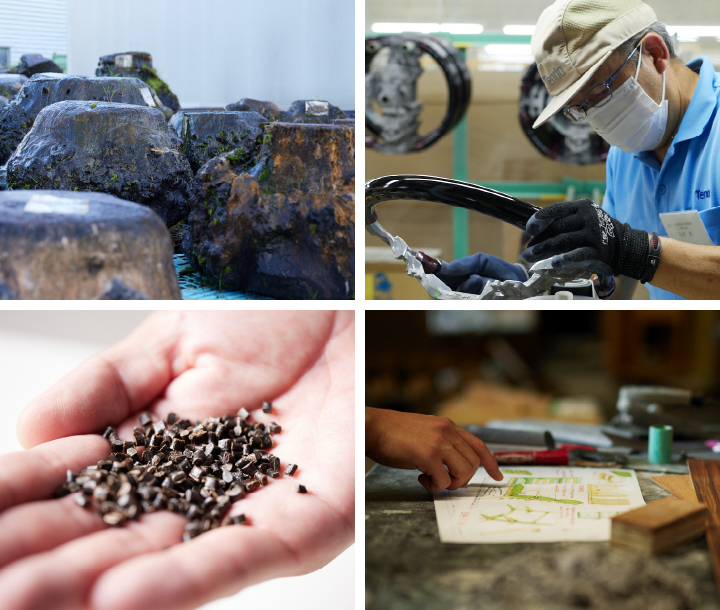
自動車内装部品・技術開発に関するお問い合わせ
天然木を使った自動車内装部品のご依頼、
カーボンニュートラル・サスティナブルマテリアルとして期待される
改質リグニンやセルロース系繊維を使用した環境にやさしい技術開発に関するご相談など
お気軽にお問い合わせください。