Products made today in Tendo
―for the next generation to treasure
Tendo City is right in the middle of Yamagata Prefecture in the Tohoku area of Japan.
Tendo Mokko was established in 1940 in Tendo,
which has long been known as a woodworking town famous
for the Japanese chess pieces it produced.
Yamagata artisans have always had a mentality that combined curiosity,
technique and the patience of the people of the North. In 1940,
techniques to use molded plywood were still new in Japan,
and it opened up a new field of furniture making in the country.
We were one of the first companies in Japan to use formed plywood to
mass-produce good-quality furniture.
Today Tendo furniture is still durable and easy to use,
but we have expanded to collaborate
with top Japanese architects
and designers to create complicated curved lines
impossible with natural wood.
When we at Tendo consider excellence in furniture,
we imagine family assets original owners can hand down to the next generation.
Tendo delivers furniture that parents will want to pass on to their children,
who will in turn leave it to their own children.
Product Features
Beautiful furniture is nothing less than a valuable possession you leave to the next generation.
To create furniture that can be treasured and used for many years,
Tendo was one of the first companies to put formed plywood techniques into practical use.
The four features listed below are all the result of our experience making furniture
that adds to the quality of their owners’ lives.
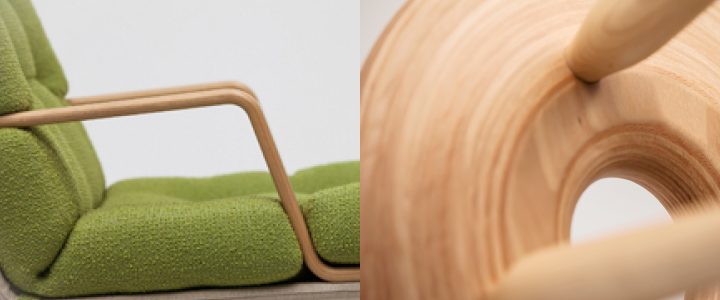
Graceful Strength
Wood that tries to take an unwavering stand can be knocked over in a stiff wind. Supple, flexible trees, like the willow, remain standing. They have the “graceful strength” to absorb impact, and this is the secret of formed plywood, although it doesn’t start out that way. When plywood is made, all material that might split or break is removed. Artisans carefully consider the characteristics of the original wood and put it through test after test to finally come up with the optimal width and thickness. A good example is our S-5226 rocking chair, which is made from a single piece of plywood except for the armrests. To keep the legs of the chair strong, a piece of wood is fitted into the plywood using a technique called “adding a piece” forming.
This unique woodworking technique is proof of the serious attitude our artisans bring to their work. The added strength is a basic function of furniture used for generations.
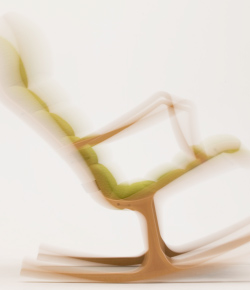
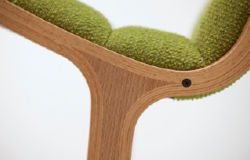
Beauty
Plywood was created as a way to mass-produce high-quality furniture. Tendo Mokko, one of the first companies to use it in Japan, was not interested exclusively in mass production, but also in beauty of products. Isamu Kenmochi and Sori Yanagi, respected designers, and Kenzo Tange, and other world-class architects were intrigued and inspired by plywood, which was thin but strong and could be crafted into curves and other complicated forms in ways impossible for natural wood. Their tireless pursuit of beauty was the force behind “3D press forming” and “adding a piece forming,” which adds strength to beauty, and other high-level artisanal techniques. Beauty is another important aspect of furniture that can be passed down from generation to generation.
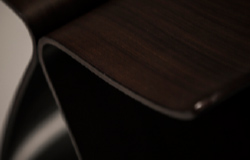
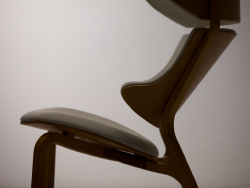
Lightweight
The word “furniture” covers a huge range of shape and usage. For example, display cabinets in the living room are almost never moved, but chairs are pulled forward and moved back as people sit down and stand up again. They are also repositioned for cleaning. When choosing chairs, comfort and beautiful design are of course important, but so is being light enough to easily move. Making heavy furniture is never a problem, but it takes a good deal of technique to make pieces that are durable but lightweight. The plywood used by Tendo Mokko is strong, but not much is needed, so it is much lighter than natural wood. Lightweight furniture cuts down on stress for excellent function.
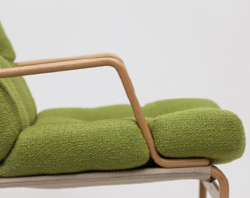
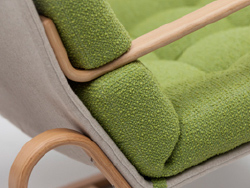
Texture
Furniture gets touched whenever it is used. It won’t make a good impression if wood feels rough or it is poorly upholstered. We at Tendo Mokko make sure our products feel good to the touch. Most furniture is painted and polished 4 to 8 times, but Tendo Mokko does more, whether it is for items for the Imperial Household or to furnish buildings designed by famous architects or for the homes of our regular customers. There is no difference in quality. Yamagata artisans have always been known for working in an honest, straightforward way, and we have inherited that valuable mentality.
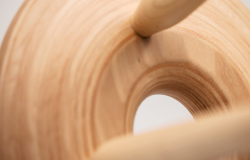
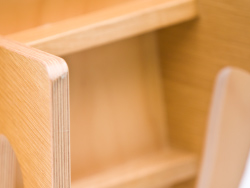
Behind Tendo’s Pride of Work
Just like people, trees come in different varieties and have their own personalities
when it comes to strength, color, and grain.
The first step to making furniture our customers will love for a lifetime begins
with a conversation to get to know the tree we’ll be working with.
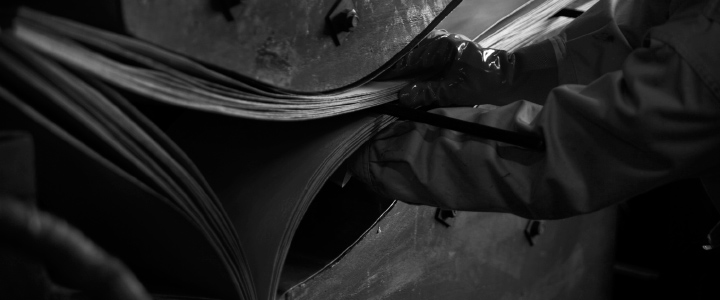
Taking time to bring out a tree’s special qualities
Walnut, rosewood, oak, sapele, white beech. Tendo Mokko gets supplies of wood from all over the world, so customers can choose. All lumber is dried naturally over one to five years. Yes, we purchase wood and just leave it for up to five years. It doesn’t seem to make sense efficiency-wise, especially in our speed-driven society. But wood grows in nature, and at a slow pace. In order to use wood to make furniture, we leave it in an environment with the same rhythms it was raised in to avoid stress and slowly remove moisture. If we put priority on speed and efficiency to dry it, it might split or bend, meaning we’d have to dispose of much more of it. Trees are “cooperative” in relation to the time we give it. This is what we at Tendo Mokko have learned from the wood we work with.
High-level artisanal technique creates durable, beautiful furniture
Plywood was first used to make furniture in 1930. Tendo Mokko began using it in 1947, seven years after the company was founded and right after the end of World War II. It was one of the first Japanese companies to make practical use of the material. Many thin layers of wood are glued together, inserted into a jig(a different one for each type of product) and then formed with heat and pressure in an enormous press. The explanation may sound simple, but all of the work is done by hand.
The formula for glue can vary depending on the weather. The layers of wood are fitted to be perfectly even when finished, and then carefully inserted into molds. Pressure is applied just so to make sure the wood doesn’t split or wrinkle. It is a complicated task that requires a high level of technique. In fact it is this technique that creates the beautiful, soft curves that are impossible with natural wood. Wood must be thin to form furniture that is ideal in terms of strength, weight and beauty. It is what we at Tendo Mokko, even after decades of polishing our expertise, aim to achieve with every single piece we make.
Making furniture from domestic conifers
Sixty-seven percent of Japan is covered in forest. As the saying goes,
“raise a forest and live on its bounty.” Coexisting with the forest is
something Japanese have been doing for thousands of years.
Forests here, however, are in crisis due to deregulation of the lumber industryand a decline in forestry.
When we thought about what Tendo Mokko could do in this situation,
we decided to breathe life into Japanese forests and the forestry industry by using conifers,
like cedar and Japanese cypress, to make good-quality furniture.
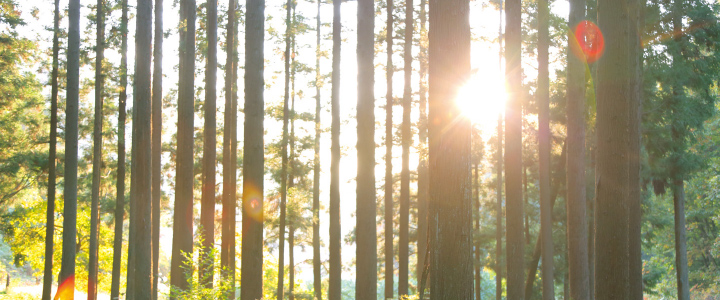
Weak points of conifers covered
with new compaction processing techniques
Conifers, such as cedar and Japanese cypress, are used mainly as columns and flooring. But since the wood is soft and easily scratched, it undergoes compaction with a press so it can be used as a surface material. It also needs to be strengthened and hardened. For this, it undergoes compaction, a common technique in making construction materials, one that broadens possibilities for soft conifers. On the other hand, since it was developed for flat surfaces, heating can burn the top and it was not originally considered suitable for processing intricate patterns. The first step to solving the problem was when Tendo Mokko put its own plywood forming technology into practical use in Japan, something the company has continued to perfect.
Tendo Mokko makes its furniture using thin layers of wood that are layered together and formed by putting them into a press and adding pressure and heat, and we have developed a new type of compaction technology that requires less heat and shorter time in the press so that the wood can be formed into just the right thickness. This new technique leaves a clean wood grain that looks good and is easy to process.
Using wood production techniques
to make interior furnishings for cars
In 1987, Tendo began making panels for automobiles using natural wood.
We have continued our research and development in this field,
and our products have been used by Honda, Toyota, Nissan, and Isuzu.
Most panels you’ll see are printed with a wood grain and not made of natural wood,
but Tendo uses valuable wood that is worked by artisans completely by hand.
Natural wood creates a very special feeling and an exquisite, luxury car interior.
Along with natural wood, Tendo is now making interior furnishings with other materials,
such as carbon cloth, and Tendo technique and knowhow can be found in many other products,
such as musical instruments and smartphone cases.
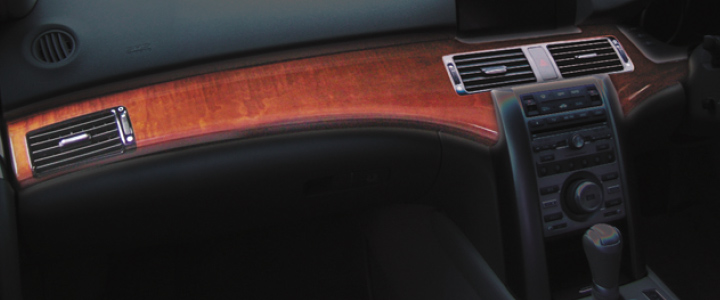
Showroom&Store
Tendo has showrooms of furniture for homes and businesses at our Head Office in Yamagata,
and in Tokyo and Osaka. The Head Office showroom includes our wooden parts for automobiles.
Come and see coordinated room sets and talk to staff about choosing furniture.
We look forward to seeing you!
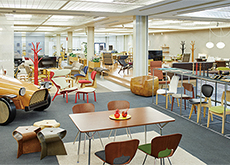
1-3-10 Midaregawa, Tendo, Yamagata
TEL 0120-01-3121
FAX 023-653-3454
E-mail:info@tendo-mokko.co.jp
9:30 a.m. to 5:00 p.m.
10 min. by car from JR Tendo Station.
10min. by car from Tendo I.C.
on the Tohoku Chuo Expressway
Tax-free Shop
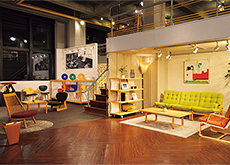
1-19-2 Hamamatsu-cho,
Minato-ku, Tokyo
TEL 0120-24-0401
FAX 03-5402-6469
E-mail:t-tokyo@tendo-mokko.co.jp
10:00 a.m. to 5:00 p.m.
*Wednesday and holidays are closed.
3 min. walk from North Gate of
JR Hamamatsu Station
3 min. walk from A2 and B4 exits of
Daimon subway station.
Tax-free Shop
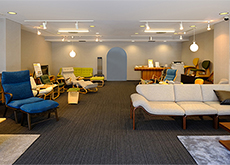
2-13-28 Minami-horie,
Nishi-ku, Osaka
TEL 0120-53-4131
FAX 06-6531-4935
E-mail:t-osaka@tendo-mokko.co.jp
Weekday : 10:00 a.m. to 5:00 p.m.
Weekend : 11:00 a.m. to 6:00 p.m.
*Wednesday and holidays are closed.
10 min. walk from Exit 6 of the
Yotsubashi subway station
6 min. walk from Exit 3 of the
Nishiohashi subway station
Tax-free Shop
1-3-10 Midaregawa, Tendo, Yamagata, Japan 994-8601 | |
Established | 1940 |
---|---|
Products |
Order-made wooden furniture Formed plywood furniture Wood parts for automobiles |
Branches | Tendo, Tokyo, Osaka, Fukuoka, Nagoya |
Certification | ISO 9001:2008(Head office, factory) |
Phone | +81 23 653 3121 |
Fax | +81 23 653 3454 |
info@tendo-mokko.co.jp | |
URL | https://www.tendo-mokko.co.jp/ |